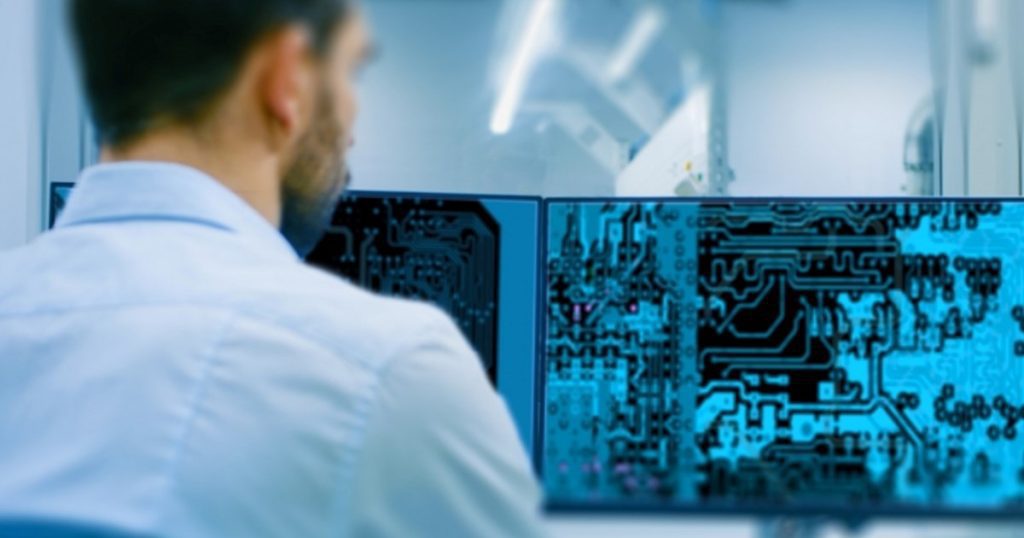
Designers need to consider many aspects throughout the electronic product design process. As an electronics manufacturer, we often come across cases where production factors have been left to last and occasionally not considered at all. We thought that it would be helpful to pick our engineer’s brains for advice on PCB design for production and assembly. Here are six top tips to help you get it right first time.
- Well designed component footprints reduce problems during solder assembly.
- Where possible use nominal density IPC-7351B/C compliant footprints.
- Do not ignore placement courtyards – they are specified for a reason, allowing space for assembly and, if required, rework.
- For components taller than 10mm consider leaving at least an extra 0.5mm between adjacent courtyards.
- Rounded rectangular pads help release solder paste from the stencil.
- Try to avoid mixed footprint rotations within a library.
- Minor changes in PCB size can have a significant effect on panel efficiency, which directly affects cost.
Know your PCB suppliers preferred raw material size. Not all suppliers are the same. To demonstrate the above you should consider the following example.
Your PCB supplier offers two standard panel sizes:
- 406mm x 508mm (356mm x 458mm working area)
- 305mm 457mm (255mm x 407mm working area)
With an original design size of 181mm x 147mm, 3up on the first panel offers 65% efficiency and 2up on the second panel offers 51% efficiency.
With the final design reduced to 175mm x 147mm, you could achieve 94% efficiency with 6up on the first panel.
- Getting panel layout right aids problem-free assembly.
- Understand how your PCB supplier steps data and where possible allow them the freedom to optimise panel layout.
- Bigger panels are not always better; smaller panels are easier to handle for inspection and rework (if necessary).
- Step patterns should allow a minimum of 2mm between adjacent boards (the width of a standard routing tool). However, 6mm between adjacent boards offers a more rigid panel.
- Tab routing gives a smooth finish – using inset perforated tabs will ease breakout and may remove the need for sanding the board edge.
- Ideally, keep all copper 1mm from the PCB edge, although 0.5mm is ok.
- Try to keep components at least 2mm from the PCB edge to avoid damage during PCB breakout.
- V-score breakouts are not as precise as tab routing.
- Keep all copper 1mm from the top of a v-score.
- Keep all components 2mm from the top of a v-score.
- Add three global fiducials in the corners of the panel border.
- Getting PCB design right aids problem-free assembly.
- Aim for a balanced build with respect to layer count and copper distribution, this avoids warping.
- Multilayer PCBs should have even layer counts.
- Clearly specify copper weight and preferred PCB finish.
- Add three Fiducials to corners of the PCB.
- Aim for a common component orientation.
- Reduce the number of different components where possible.
- Use surface mount components if possible.
- Avoid using silkscreen for small components
- Try to keep all components on the primary side.
- If the design is double-sided, large components should be on the primary side only.
- Ensure the board has a part number and issue marked on it.
- On thicker boards consider the aspect ratio and try to avoid greater than 8:1
- For very fine pitch components consider local fiducials.
- Ensure any impedance control requirements are clearly defined.
- Clear, detailed BOMs can save time and money.
- Only specify a specific manufacturer where it is critical to the design. Your manufacturer may be able to offer lower cost alternatives with shorter lead-times.
- Clearly define any components that should not be fitted.
- If the design has variants, these must be clearly defined, ideally with a separate part number or issue control.
- Cost can be controlled by avoiding overspecification.
- As layer count increases, so does cost.
- As feature sizes reduce, price increases.
- Minimise/optimise drill sizes.
- Advanced features, such as blind vias, will increase cost.
- Define IPC-A-600 / IPC-A-610 Class 2 or 3 – do not over specify.
There’s a lot to consider, even within this limited list, but getting design for production right will pay off with lower cost, faster lead-times, and a higher quality outcome. If you have any questions about PCB design for manufacture, our engineers are always on hand to help.
Give us a call today on 01425 655655