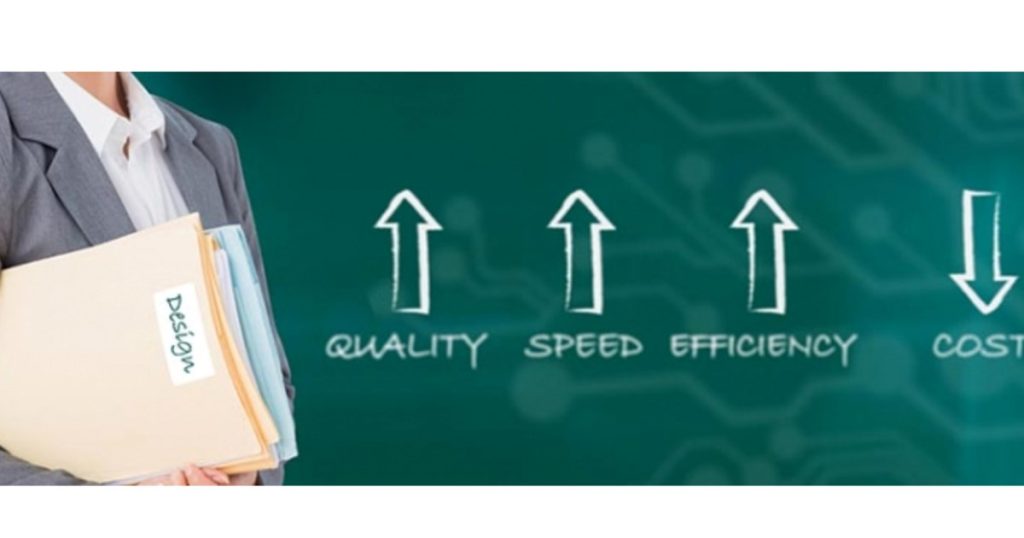
In this article, we are going to outline the key issues a Contract Electronics Manufacturer (CEM) may face when preparing your product for manufacture. We’ll detail how you, as a customer, can help in avoiding these issues and ensuring processes run as smoothly as possible by defining some best practice DFM tips. By ensuring that your design files contain all required and correct information, you help enable the most efficient and accurate preparation of your product’s manufacture, as well as improve the delivery time and quality of the final product.
Creating a robust, accurate and effective Design For Manufacture file requires a little time and strong attention to detail, but will almost always save time in the long run. Documentation usually requested by a CEM as part of the design for manufacture (DFM) process can include; all details related to the PCB, the assembly work required, the materials required, design schematics, test procedures (if any) and any special manufacturing instructions the design may require.
Benefits of a robust Design For Manufacture file include:
● More time for you to focus on your next projects – the more concise the information you provide, the fewer queries your CEM will have for you and the less they will need to interfere with your day!
● Lower cost – getting production right the first time around means no extra costs required to fix design information problems
● Faster turnaround – with little to no issue, your product can be manufactured as quickly as possible
● Higher quality product – precise, accurate design files ensure that products are built to the correct standard and highest level of quality every time
We’ve sat down with our engineers to outline the most effective ways of creating the most robust design for manufacture file. Over the next few news features, we will dive into discussing the most critical obstacles when designing for manufacture, to ensure the smoothest of processes for both you and your CEM.