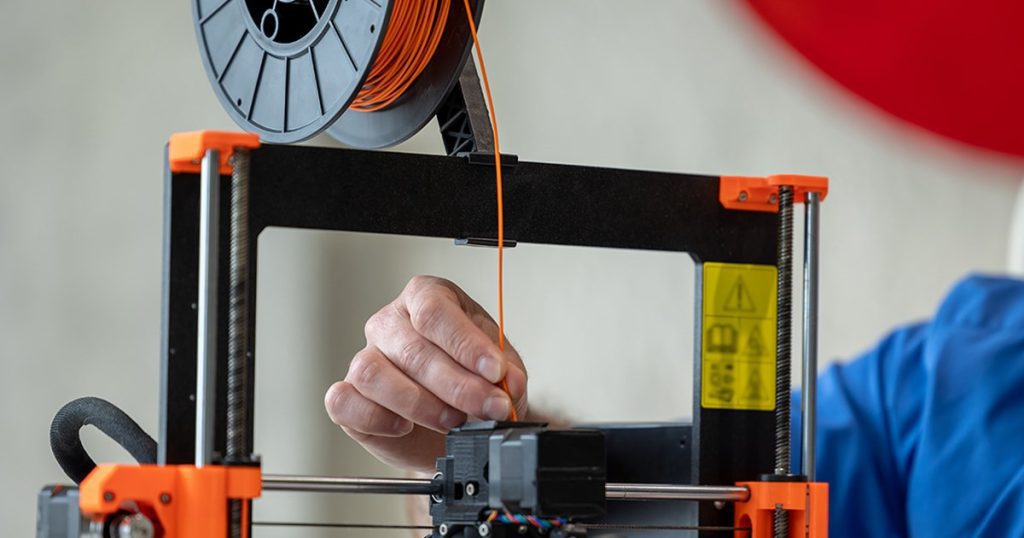
At Corintech, we use Stereolithography and Fused Deposition Modeling printing – allowing us to discover and correct flaws while undertaking extensive testing prior to the final production stage. 3D printing in its traditional form is frequently associated with environmental concerns due to waste generation and reliance on plastic materials. However, at Corintech, we are firm believers in using the benefits of 3D printing in the design process to ensure the ultimate quality of our products.
What is Stereolithography (SLA)?
SLA (Stereolithography) printing technology. SLA is a type of 3D printing or additive manufacturing process that uses a photopolymerization technique to create three-dimensional objects. Due to its exceptional precision and level of detail, SLA printing is a great option for producing complicated and detailed parts, prototypes, and patterns. It’s frequently utilised for small-scale production, product development, and quick prototyping in sectors like engineering, healthcare, automotive, and aerospace. The technology makes it possible to create items with a smooth surface finish that are accurate and high-resolution.
Here’s how it works:
- Liquid Resin: In SLA printing, a liquid resin is used as the raw material. This resin is typically photosensitive, meaning it changes its properties when exposed to ultraviolet (UV) light.
- Layer-by-Layer Process: The printing process occurs layer by layer. A platform is submerged in a tank of liquid resin, and an ultraviolet laser is directed at the surface of the resin. Wherever the laser strikes, the resin solidifies and hardens.<?li>
- Layer Formation: The platform is gradually lifted out of the resin tank by a small distance, and the laser continues to trace the cross-sectional shape of the object, solidifying one thin layer at a time.
- Solid Object Creation: This process of solidifying one layer after another is repeated until the entire object is formed.
- Post-Processing: Once the printing is complete, the object is typically rinsed to remove excess, unreacted resin. It may then undergo further curing under UV light to ensure all the resin is fully composited.
What is Fused Deposition Modeling (FDA)?
Here's how it works:
- Material Filament: FDM 3D printers use a thermoplastic filament, usually in the form of a spool. Common materials include PLA, ABS, PETG, and more.
- Heating and Extrusion: The filament is fed into a heated extruder, which melts the plastic material. The extruder nozzle is then moved in the X, Y, and Z axes to deposit the molten material layer by layer onto a build platform.
- Layer-by-Layer Building: The object is built up layer by layer. The platform typically moves down or the nozzle moves up after each layer is deposited. This process is repeated until the entire object is created.
- Cooling and Solidification: As the extruded material is deposited, it quickly cools and solidifies, creating a stable structure for the next layer to adhere to.
- Support Structures: In cases where an object has overhangs or complex geometries, support structures may be added. These are temporary structures that can be easily removed after printing is complete.
Why has Corintech introduced FDM?
Recognising the environmental problems, we’ve been proactive in looking for ways to reduce the carbon impact of our 3D printing. In this regard, we’ve made tremendous progress by using recycled, non-virgin plastic in our prototypes. This strategy shift is part of our ongoing effort to improve sustainability by making our FDM prototypes more ecologically friendly. While standard 3D printing is not intrinsically environmentally friendly, we are committed to developing creative and sustainable solutions that allow us to strike a compromise between design excellence and environmental responsibility. Corintech is on a mission to ensure that our commitment to quality is in sync with our commitment to a greener, more sustainable future. Thus, as this technology constantly evolves, we are excited to see what other changes we can make in the future!