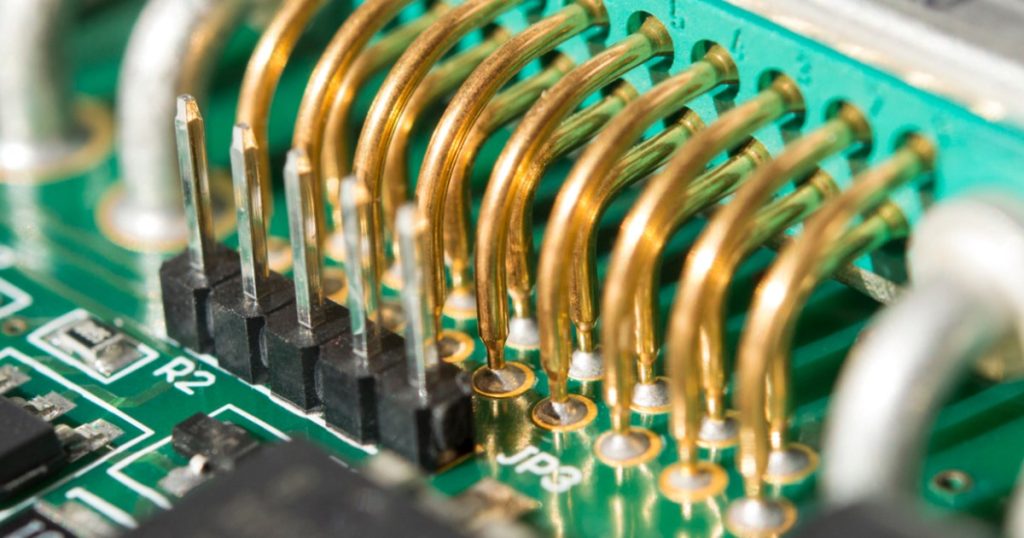
IPC-A-610 is a crucial standard for ensuring the quality and reliability of electronic assemblies. In this article, we provide an updated overview of IPC-A-610, explain its importance in electronics manufacturing and discuss how it should inform your procurement process.
What is IPC-A-610?
IPC-A-610 is the industry standard for acceptability of electronic assemblies. Created by IPC, it sets visual and workmanship standards for evaluating soldered assemblies.
In short:
- It defines what an acceptable PCB assembly looks like.
- It ensures consistency between manufacturers, inspectors and buyers.
- It’s often used with IPC J-STD-001, which covers soldering process requirements.
This shared framework helps reduce misunderstandings in quality expectations across the supply chain.

Why IPC-A-610 Matters
Quality and consistency are everything in electronics manufacturing. IPC-A-610 acts as a common language – whether you’re assembling boards or approving final builds.
For procurement professionals, this standard helps:
Set clear quality benchmarks with suppliers
Balance cost vs. performance by selecting the right class
Reduce the risk of defective or unreliable assemblies
The Classes Explained
The standard defines three classes, each suited to different types of electronic products:
Class 1 - General Electronic Products
Low-cost, non-critical items
Some cosmetic flaws allowed if the product works
Example: toys, basic consumer gadgets
Class 2 - Dedicated Service Electronic Products
Better durability and performance
Expected to work reliably over time
Example: office electronics, control systems
Class 3 - High-Performance Electronic Products
Must perform consistently without failure
Highest quality requirements
Example: medical devices, aerospace systems
Key Inspection Areas in IPC-A-610
IPC-A-610 outlines exactly what inspectors should look for during PCB assembly evaluation. Here’s what each area covers:
Solder joints must be correctly shaped and fully wetted. This ensures strong electrical connections across all types of components, whether surface-mounted or through-hole.
Component placement is checked for proper alignment and orientation. Misplaced or skewed parts can cause performance issues or complete failure.
Cleanliness is crucial, especially in Class 3 assemblies. Residual flux and other contaminants must be removed to avoid corrosion or signal leakage over time.
Mechanical integrity involves inspecting the board and its components for physical damage. Large components may need additional support to stay secure during handling or vibration.
Lead forming and trimming must follow precise guidelines. Leads should be shaped and cut to length without stressing the component or the board.
Conformal coating, when applied, needs to be even and controlled. The coating should protect vital areas without covering connectors or other exposed contacts.
Identification markings like reference designators, polarity symbols and version codes must be clear and accurate. These are essential for maintenance, traceability and future updates.
Each of these areas helps maintain high quality and long-term reliability in electronic assemblies.
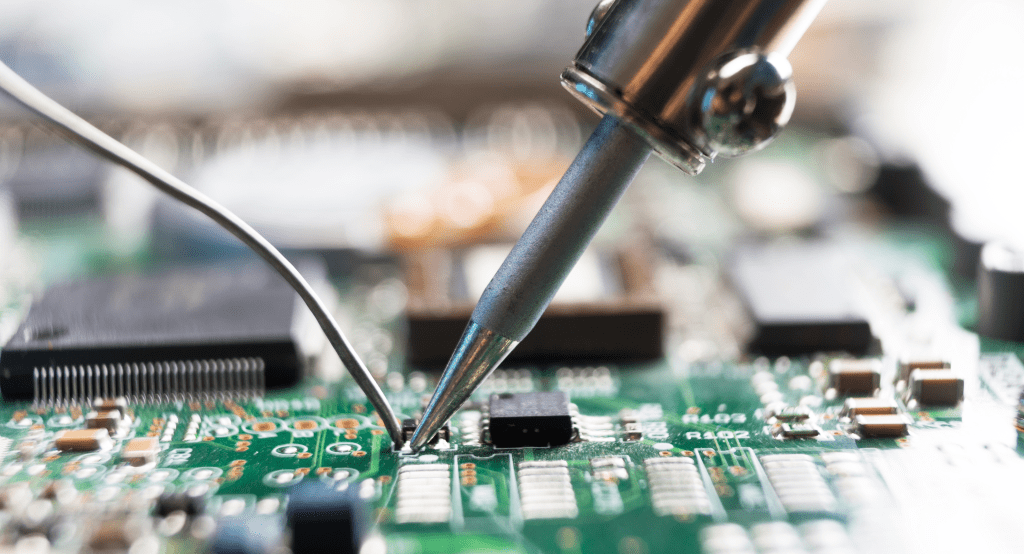
Using IPC-A-610 to Make Better Buying Decisions
Understanding IPC-A-610 gives procurement teams a clear edge. Here’s how you can apply it:
Ask the right questions:
“What IPC class do you build to?”
“Do you follow J-STD-001 for soldering?”
Request documentation
Class specifications
Inspection records
Any certifications (e.g. IPC-certified inspectors)
Specify clearly
Mention the IPC-A-610 class in your documentation
Match the class to the intended use of your product
This approach helps avoid miscommunication and ensures your chosen manufacturer delivers what you need, nothing more, nothing less.
Why Choose Corintech?
At Corintech, we manufacture assemblies up to IPC-A-610 Class 3 – the highest quality level.
Trusted for medical, aerospace and industrial builds
Experienced team trained to IPC and ISO standards
Rigid process controls and continuous inspection
Need to discuss your project? Get in touch with our team to explore how we can meet your technical and quality needs.
Final Thoughts
IPC-A-610 continues to play a key role in modern electronics manufacturing. For engineers and buyers alike, it’s more than just a document, it’s a shared expectation of quality and reliability.
By specifying the right class and working with experienced suppliers, you can:
Improve product performance
Avoid costly rework
Strengthen customer confidence
Want a partner who takes quality as seriously as you do?
Corintech is here to help.